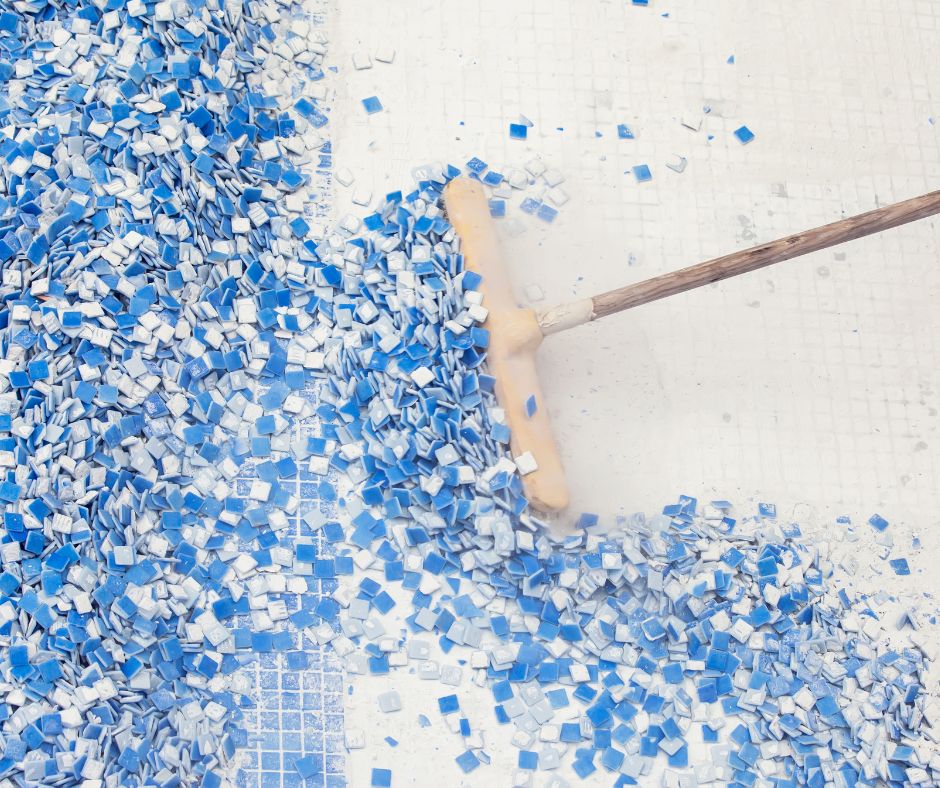
When it comes to enhancing the look of your backyard,investing in a pool resurfacing project can be a game-changer. However,understanding pool renovation costs and budgeting for your pool accordingly is the key to ensuring a successful and satisfying outcome. From assessing the size and type of your pool to the selection of resurfacing material,every aspect contributes to the overall expense.
Pool resurfacing is a necessary but significant investment for pool owners. Every pool,regardless of its type,requires resurfacing at different intervals due to wear and tear from pool chemicals,weather conditions,and usage. The entire process could be daunting,especially when you consider the cost involved. Therefore,it’s essential to understand the various components that determine the pool resurfacing costs.
What Determines the Cost of Pool Resurfacing?
The cost of pool resurfacing is influenced by numerous elements. The pool size is one primary factor,as larger pools require more materials and labor,hence leading to higher pool resurfacing costs. The type of finish you select – plaster,paint,aggregate,or tile- also plays a significant role in the final cost,with prices for these finishes ranging from $1.50 to $25 per square foot. Additionally,preparation work like cleaning and repairing any damage before resurfacing adds to the overall cost. Let’s not forget the labor costs,which average between $45 and $65 per hour and could be potentially higher in urban locations.
You need to know all aspects of pool renovation and read more here,including understanding the pool project cost and budgeting for pool resurfacing.
Average Costs and Range for Pool Resurfacing
Understanding the average pool resurfacing cost in your locality can be incredibly insightful in your pool cost breakdown. For instance,resurfacing a fiberglass pool averages around $6,500 per 1,000 square feet. However,each job is unique and can vary based on many factors,which creates a wide cost range. Here’s a table to give you an approximation:
Type | Average Cost |
---|---|
Fiberglass | $6,500 to $15,000 per 1000 sq.ft |
Plaster | $4,000 to $5,000 per 1000 sq.ft |
Paint | $1,500 to $3,000 per 1000 sq.ft |
Aggregate | $5,000 to $10,000 per 1000 sq.ft |
Tile | Varies based on type and design |
Paying attention to these factors is crucial to managing pool maintenance costs. By developing a comprehensive understanding,you can plan your finances effectively,avoiding unnecessary surprises during the course of your pool resurfacing project.
Budgeting for Your Pool: Project Expenses Breakdown
When it comes to resurfacing your pool,understanding the various pool expenses involved can make all the difference. Here we’ll be providing some essential pool budgeting tips and a comprehensive project expenses breakdown to guide you in making the most financially sound decisions for your pool project.
Cost of Materials
Firstly,the cost of materials plays a significant role in your overall expenses. A traditional plaster finish,for instance,costs around $4 per square foot,while a more durable pebble finish is priced at approximately $10 per square foot.
Draining and Cleaning
Next,one significant cost to consider is the process of draining your pool,which stands at an estimated cost between $175 – $225. Plus,once drained,it would need cleaning,setting you back about $250. The cost of refilling your pool might seem inconsequential,but it hovers around $55 for every 5,000 gallons of water,which can add up fast depending on your pool’s size.
Labor Charges
The labor charges can significantly differ depending on your location. Still,they usually range anywhere from $45 to $65 per hour,and this certainly adds up over the duration of the project.
Additional Features
Moreover,additional features such as lighting,heaters,decking,or fencing can significantly elevate the cost. Here’s a simple breakdown:
Feature | Estimated Cost |
---|---|
Basic Lighting | $20 and up |
Heaters | $2,100 – $3,500 |
Decking | $1,500 – $ |